Delivering the World's
LEADING EVENTS
TO THE WORLD'S BUSINESS LEADERS
Find an Event
EVOLVING YOUR EVENT EXPERIENCE
IQPC goes beyond the traditional physical and virtual event experience to deliver enhanced learning and networking opportunities. We offer blended digital learning through our extensive library of white papers, webinars, videos, case studies, and tailored research to keep you ahead of your industry. Our B2B digital communities extend your networking beyond the event to over 1 million members. Our combination of digital content, real world events, virtual events and online communities provides unrivaled learning, network and sponsorship opportunities.
Digital
learning
Access articles, case studies, white papers, infographics, podcasts, and videos addressing your specific industry challenges.
Start Learning NowEvents &
Conferences
Choose from over 1,200 conferences, exchanges and exhibitions from around the world.
Search Events NowFEATURED EVENTS
JOIN OUR ONLINE COMMUNITIES
Find new connections, discover new thought provoking research and solve your
industry specific challenges in your dedicated online community.
DIGITAL CONTENT SPONSORSHIP
Are your sales teams demanding more qualified leads?
Are you struggling to develop thought leadership ideas to engage customers and prospects online?
Are you having trouble building an effective online strategy?
Are your social media channels failing to deliver ROI?
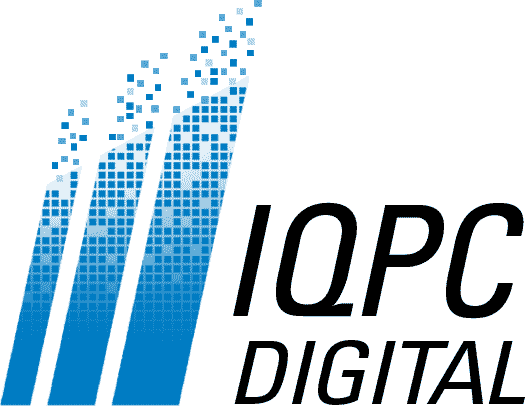
EXCEEDING EXPECTATIONS EVERY TIME
Listen to some testimonials from past customers!
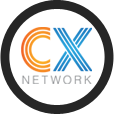
CX BFSI Exchange, USA
Customer Service
Development Mananger
BP OIL
"A fantastic opportunity to stop and step outside an insular approach to listen and understand the huge array of opportunities and innovation being created by others within the retail sector and in turn sharing and acting upon this wonderful insight received back in the day job!”
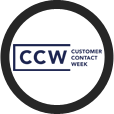
Customer Contact Week
DELIVER WORLD-CLASS SERVICE WITH SPEED & EFFICIENCY
“Started in 1999 as Call Center Week, CCW is the world’s largest customer contact event series. With the balance of conference and expo, CCW is the place where customer care, CX, and contact center leaders come together."
EVENT SPONSORSHIP OPPORTUNITIES
Your sponsorship gives you the chance to personally interact with new customers during their purchasing journey. Our customizable sponsorship packages allow us to match your solutions with customers who are actively seeking help. Sponsoring an IQPC event allows you to:
- Create new customers
- Develop qualified leads
- Convert leads into sales
- Retain customers
KICKSTART
YOUR
CAREER
Join the team that’s consistently pushing the boundaries of innovation in the world of conferences, exhibitions and digital learning.
Because with locations on 6 continents, events in dozens of industries & multiple online communities...